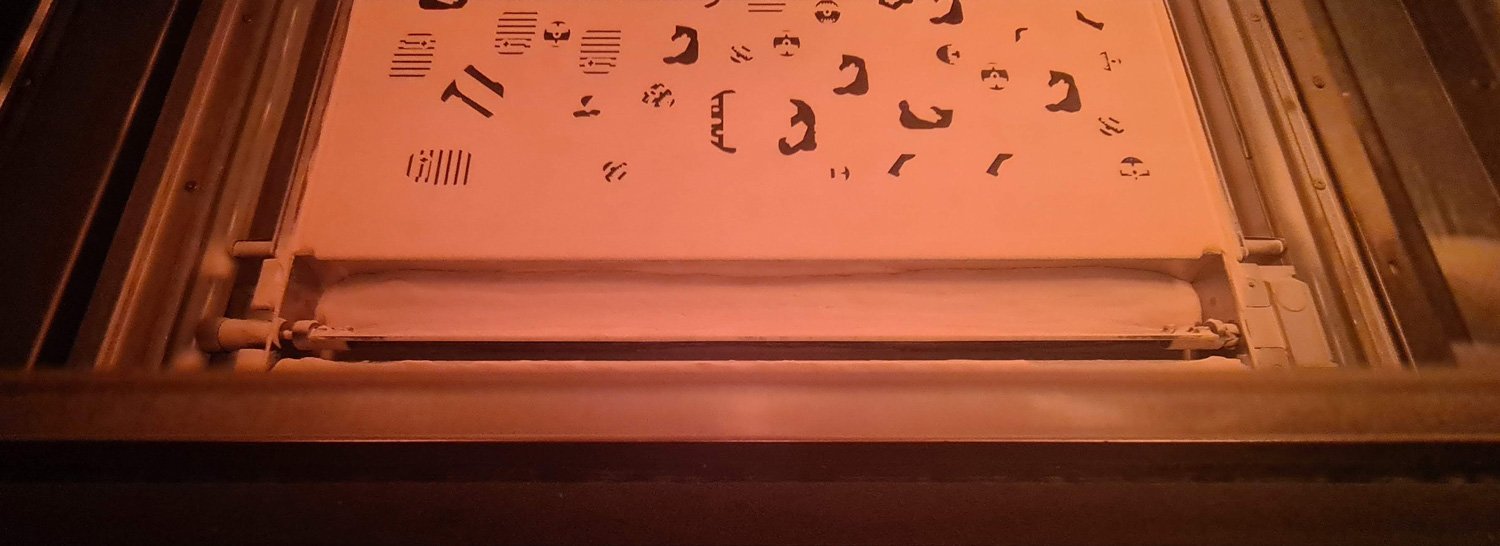
FINISHING.
Our finishing options take MJF 3D printed to the next level.
Whilst the ‘natural’ grey finish of MJF is perfect for many hidden or non cosmetic parts, it’s our dyeing, shot peening and Cerakote options that give colour and surface finish to rival injection moulding.
Stages of finish:
After being removed from print, unfused powder still attached.
After blasting to remove powder. The part has full mechanical properties. Only the first few surface microns are grey, the core of the part is solid black.
After dying. The finish is matt black and slightly porous.
After shot peening. Parts have a low sheen with a light texture similar to many consumer products. The surface has been hardened and has a high scratch resistance.
Shot Peening
We use a DyeMansion PowerShot S to ‘shot peen’ parts which gives them a low sheen and fine texture typically associated with many consumer products.
The parts are also much more mark resistant after shot peening and unlike vibro-polishing the process does not remove material and therefore change the outer dimensions and fine detail of the parts.
Dyed Black
After powder removal we use a temperature controlled dye bath to create a deep black finish.
Did you know? MJF PA12 parts are black have black core, only a few microns of the surface are grey, so when the surface is dyed the part is then black all the way through. This is different to dyed SLS parts which if the surface is scratched or worn shows the white core.
Cerakote - Ceramic Coating
Cerakote is a very thin film coating that is ideal for colouring and enhancing the properties of 3D printed parts.
150+ standard colours plus colour matching and mixing available.
Very thin (8-25 microns), minimal change to part geometry. Threads can be coated without clogging.
UV stable / Resistant (improvement over PA12s already good performace).
Chemical resistant.
High radiant heat resistance.
Hydrophobic & Lipophobic.
Skin safe.
Contact us for a free Cerakoted MJF sample