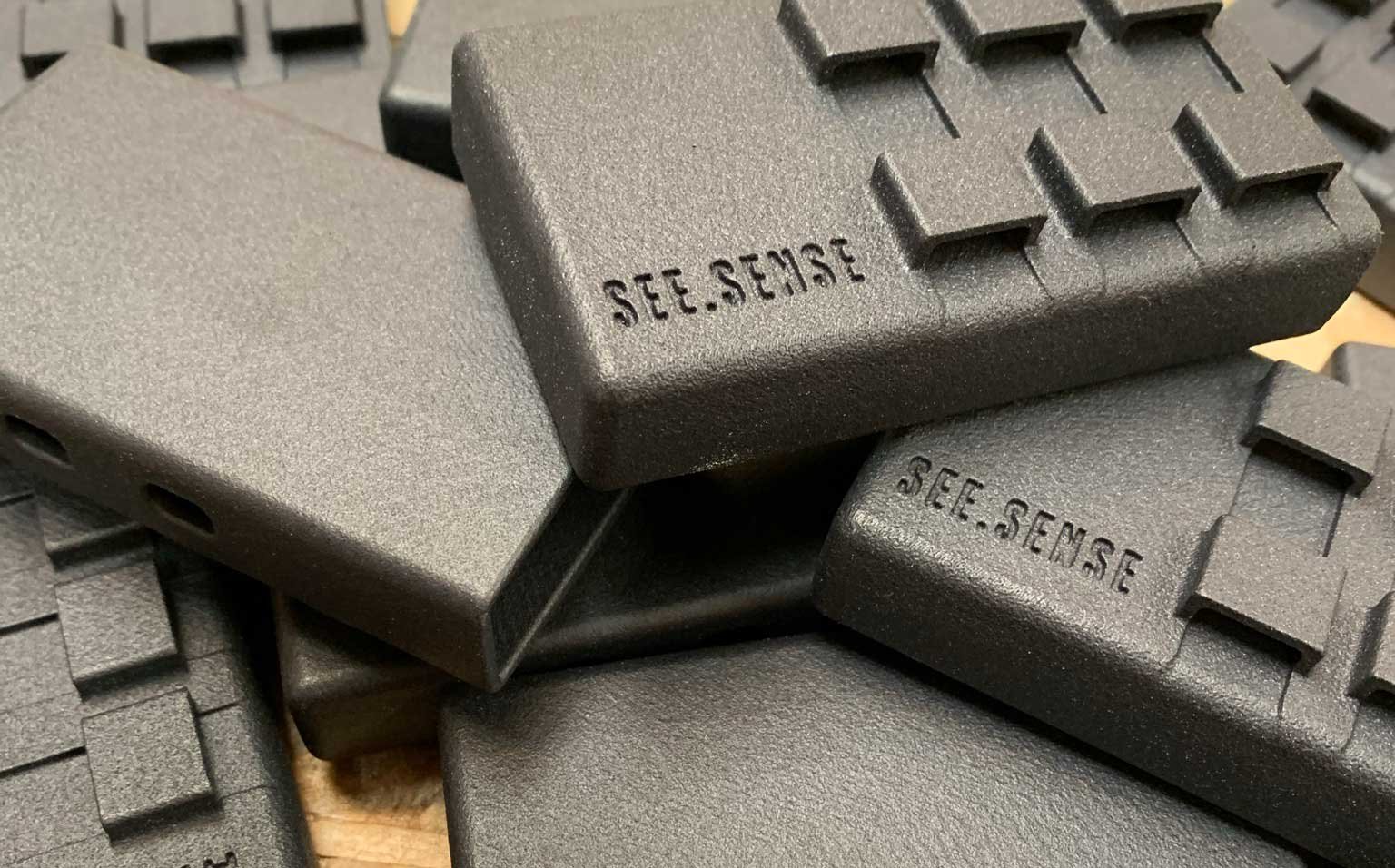
CASE STUDIES
ELECTRONICS ENCLOSURES.
Don’t be constrained to off the shelf enclosures or project boxes.
SeeSense came to us needing an enclosure for tracking devices for E-Bike and E-Scooters hire fleet. The on demand nature of additive manufacture means that each time a new city is signed up to the hire scheme a batch can be manufactured to suit the scheme size.
AGRITECH
AgriSound approached us wanting a quick turnaround solution to mounting solar panels on their devices. We designed a one piece bracket that is 50% of the cost of the original 2 piece design and delivered a prototype in 1 week from brief with 60 units delivered a week later. Subsequent production runs have also been made.
AgriSound use accoustic technology and environmental sensors that aid an optimum pollination environment, necessary for not just the survival of our future pollinators, but our farms, gardens, and planet.
ENERGY SECTOR
Long lead time for an essential handle. No problem, we printed and delivered in under a week.
AERO BARS - Olympic Gold Winning
Produced for leading cycling Aerodynamics specialists Drag 2 Zero. The bars were used by the Olympic gold medal winning British triathlon relay team.
By using an internal lattice structure the bars perform comparatively with carbon fibre ones but could be developed faster with no tooling or design constraints.
POINT OF SALE COMPONENTS
The fast moving industry of Point Of Sale display often has a choice between fabricated or injection moulded components, both have compromises. With MJF production displays can be in store in record time.
HIGH COMPLEXITY COMPONENTS
Our sister company 76 Projects produce their world leading TT Computer Mounts using MJF. The freedom of the process means that components geometry that would be near impossible using injection moulding can be used to enable the mounts to achieve unrivaled adjustability.
BRACKETS AND FIXTURES
Brackets for end products or fixtures to assisting assembly delivered in a few days.
PRODUCTION BIKE FRAME
One of the coolest projects we’ve been involved with is a kids bike frame designed by Deviate bikes.. We’re currently working with Deviate to put the frame in to production. There’s going to be some very lucky kids!
“I have had several parts built at 76 Additive and I am so impressed on many levels :
The MJF process is a real game changer...the output is amazing quality both dimensionally and aesthetically
The cost point of the process relative to the built parts and the service given is amazing.
The whole team at 76 have an engaging ‘can do‘ attitude that is so refreshing.
I have 30 years experience designing components for the injection moulding process and to date this is the best outsourced solution I have come across .”
- Nigel Gamble, Protocol.cnc Ltd